
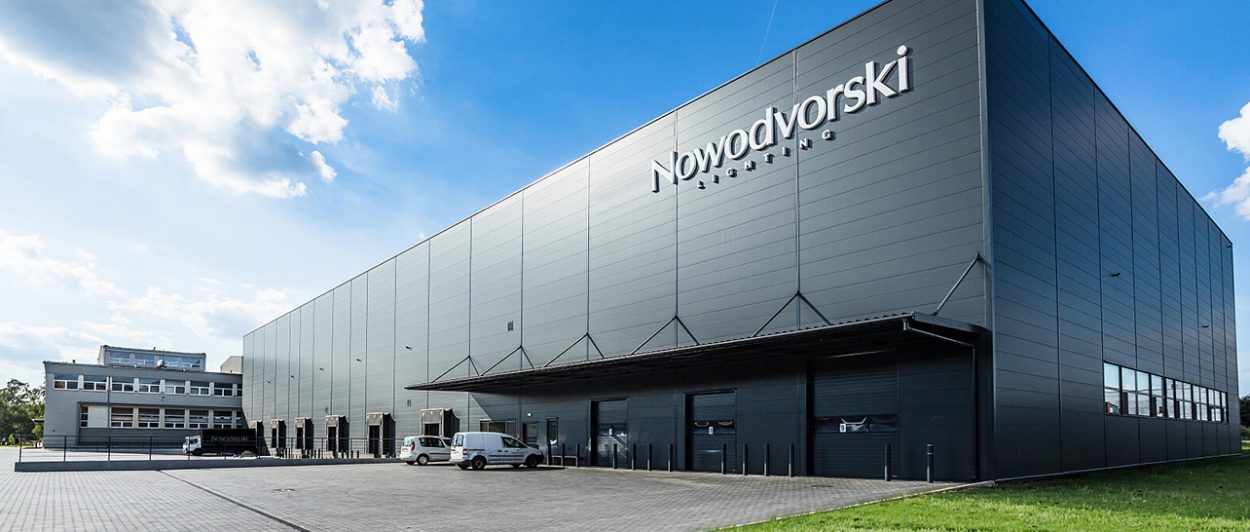
About Nowodvorski
Nowodvorski Lighting (formerly Technolux) is a family business, founded in 1994. The company’s mission is to offer a wide range of affordable, decorative lighting fixtures, dedicated to both people who value classic and modern solutions. The experience gained during 20 years of the company’s activity in the design and implementation of lighting fixtures in the production allowed it to take a leading position among Polish lamp manufacturers. Currently, the company’s offer consists of over 2.5 thousand lamp models and is updated every year with new proposals.
Efficient and quick execution of orders is guaranteed by the fact that the company’s products are manufactured in Poland. This allows you to quickly respond to changing customer needs.
Challenges
Business situation before system implementation
The company has two production plants with a total area of 12,000 m2, producing and selling 3,000 frames per day on average. Over 65% of production is sold abroad. The company exports to: Belgium, Belarus, Bulgaria, Croatia, Czech Republic, Estonia, Finland, France, Greece, Spain, Ireland, Israel, Kazakhstan, Kyrgyzstan, Kosovo Lithuania, Latvia, Malta, Moldova, Germany, Norway, Russia, Romania , Senegal, Slovakia, Ukraine and Hungary.
Nowodworski products can be purchased in the following chains: CASTORAMA, OBI, PRAKTIKER, BLACK RED WHITE and in good lighting stores throughout the country.
A large number of shipments per day and a wide range of goods resulted in the bottleneck in customer service being the process of picking and forwarding shipments in the warehouse.
Delays and errors in customer releases began to occur.
Additionally, the lack of quick and efficient communication with the order processing department and, consequently, with the production planning department, led to suboptimal stocking and lack of space in the warehouse.
Therefore, the following goals were set for the new warehouse system:
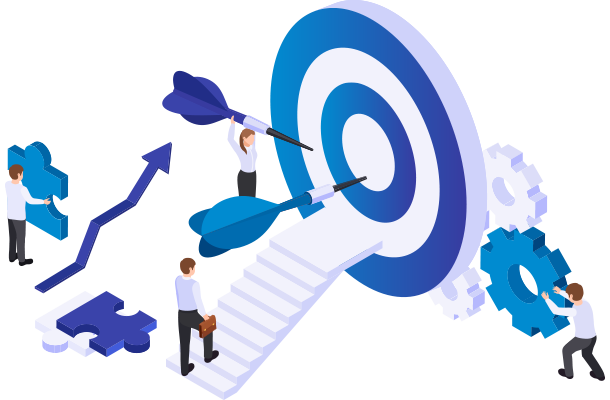
- reducing the error rate when handling warehouse orders, quick implementation of new warehouse workers
- optimization of warehouse workers’ work
- providing reliable information about the stock of goods in the warehouse
- optimization of goods arrangement in the warehouse
- optimization of warehouse stocking
- efficient handling of special products
- improving communication with the company’s sales department,
- providing an analysis of the work of warehouse workers
Solution
Nowodvorski Lighting decided to choose the RapidWMS system. ISK Sp. was selected to carry out the implementation. z o. o. – manufacturer of the RapidWMS system.
The first step in the implementation was the preparation of the Storage Program. Warehouse processes and processes in the company’s departments related to goods turnover were analyzed. The warehouse itself was also analyzed in terms of division into zones and locations, and location marking concepts were developed. At the same time, a project for the implementation of IT infrastructure in the warehouse was being prepared.
The result of the above work was a study containing the operational concepts of Nowodvorski Lighting after the implementation of the RapidWMS system.
In order to efficiently handle customer orders, changes in the company had to go much deeper and affect not only the way the warehouse operated.
The reorganization of work processes included::
- introducing batches of goods for special orders
- introducing goods reservations in the ERP system
- introduction of collective production orders based on BST analysis
- reconstruction of document flow in the sales department
In the warehouse, the changes concerned::
- wprowadzenia adresacji lokalizacji
- entering location addressing
- moving away from fixed to variable storage locations
- introduction of marked and traceable logistic units
- equipping warehouse workers with portable data collectors with the RapidWMS system
- implementation of the RapidWMS system as a management system
- work of warehousemen
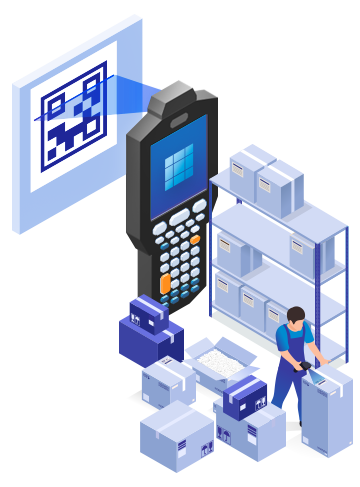
Benefits achieved
- optimization of goods arrangement in the warehouse
- more complete information for salespeople about the status of goods and the progress of warehouse orders
- quick introduction of new warehouse workers
- optimization of warehouse stocking
- reducing the error rate in warehouse releases
- elimination of paper communication with the warehouse

Customer Data:
Nowodvorski Lighting
Bojemskiego 11 St.
42-202 Częstochowa
Poland+48 34 344 91 10

Implementing company:
ISK Sp. z o.o.
Pułaskiego 25 St.
42-200 Częstochowa
+48 34 361 10 20